Our precision CNC machining delivers custom parts and components with exceptional accuracy and efficiency.
Our CNC Machining Services
CNC machining is one of the most commonly used production manufacturing processes for creating complex, customizable, highly precise, and scalable parts. At Teak Isle, CNC machining is a foundational core competency with 12 state-of-the-art CNC routers. We have the infrastructure and experience to produce high-quality, custom components CNC cut to your specific needs.
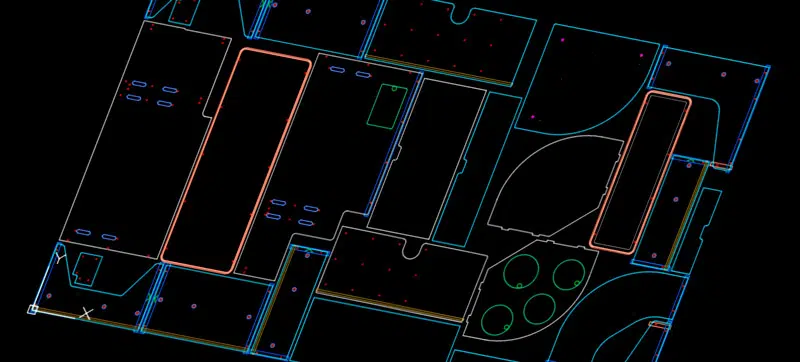
CNC Engineering
Our engineering team uses advanced nesting software to optimize sheet yield and determine the most cost-effective order multiples.
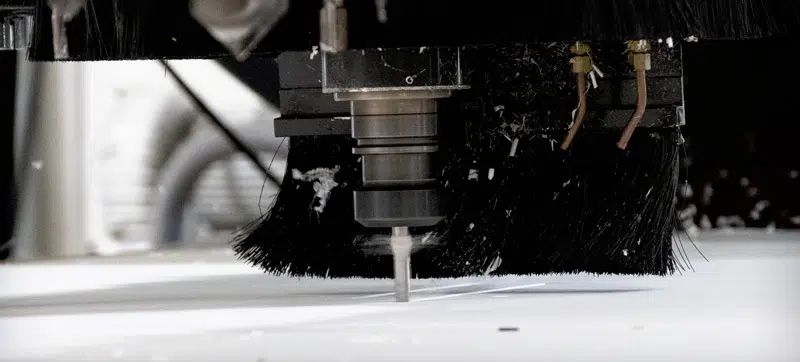
CNC Milling
We run 12 heavy-duty 3-axis CNC routers — guaranteeing quality accurate machined parts at the scale your business needs.
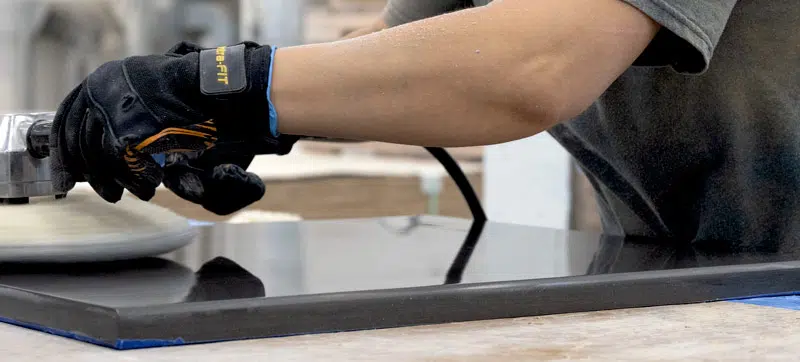
Finishing & Assembly
Post CNC Machining, we provide edge-routing, polishing, and assembly services to provide you with a ready-to-use finished part.
CNC Machining Materials
Our CNC machines cut a wide range of materials, giving you the ability to tailor solutions to meet unique product demands.
- HDPE
- Acrylic
- Expanded PVC
- Reinforced Polyurethane
- Laminated Honeycomb PP
- Flexible Vinyl
- EVA Foam
- Composite Lumber
- Solid Surface
- High Pressure Laminate
- Plywood
- MDF
- ABS
- Polycarbonate
- ACM
- Phenolic
- UHMW
- Aluminum
- Steel
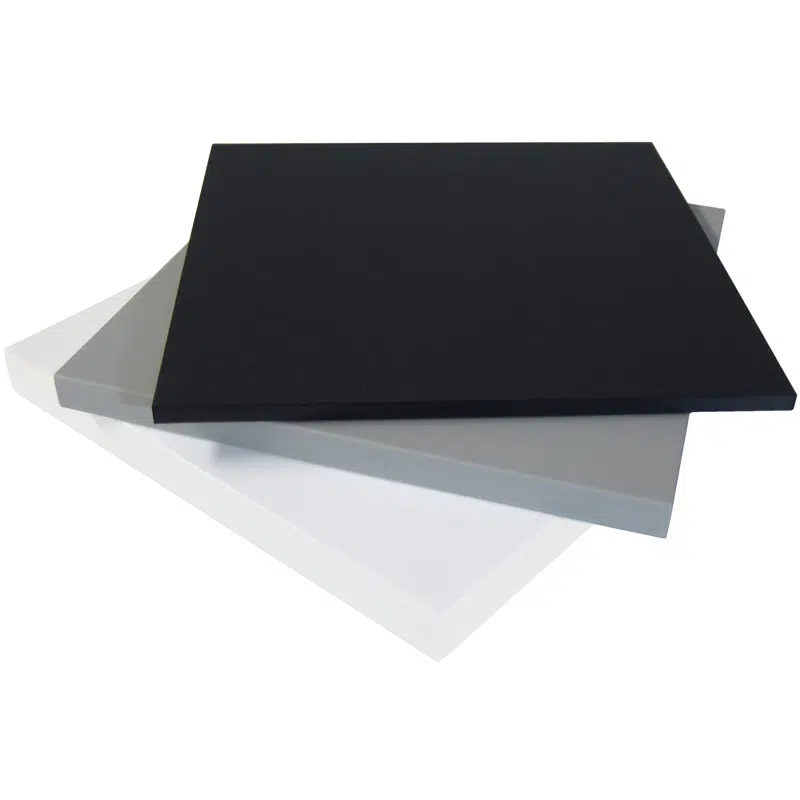
HDPE
Durable, weatherproof, and corrosion-resistant. Popular for outdoor furniture and marine accessories.
- Marine and boat components
- Outdoor furniture and playground equipment
- Cutting boards and food prep surfaces
- Exterior signage and displays
- Material handling and wear strips

Acrylic
Versatile plastic (available clear, tinted or opaque) commonly used for signage, displays, and protective barriers.
- Signage and displays
- Protective barriers and shields
- Aquariums and fish tanks
- Picture frames and photo displays
- Point-of-purchase displays and retail fixtures
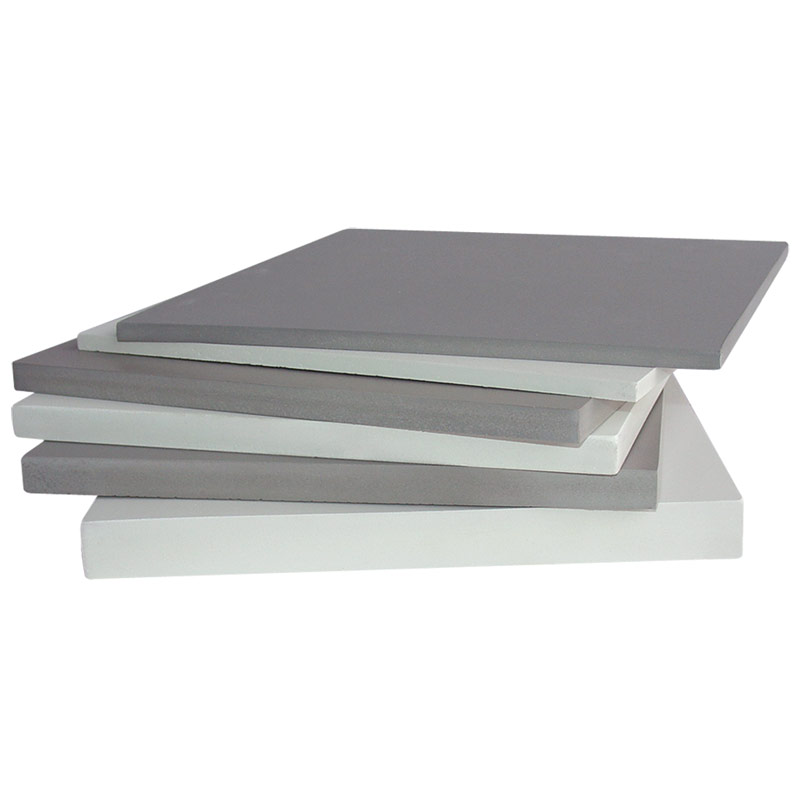
Expanded PVC
Lightweight and easy to fabricate. Great for substrates, signage and lightweight displays.
- Upholstery Substrate
- Signage for indoor and outdoor use
- Exhibit and display setups
- Thermoforming projects
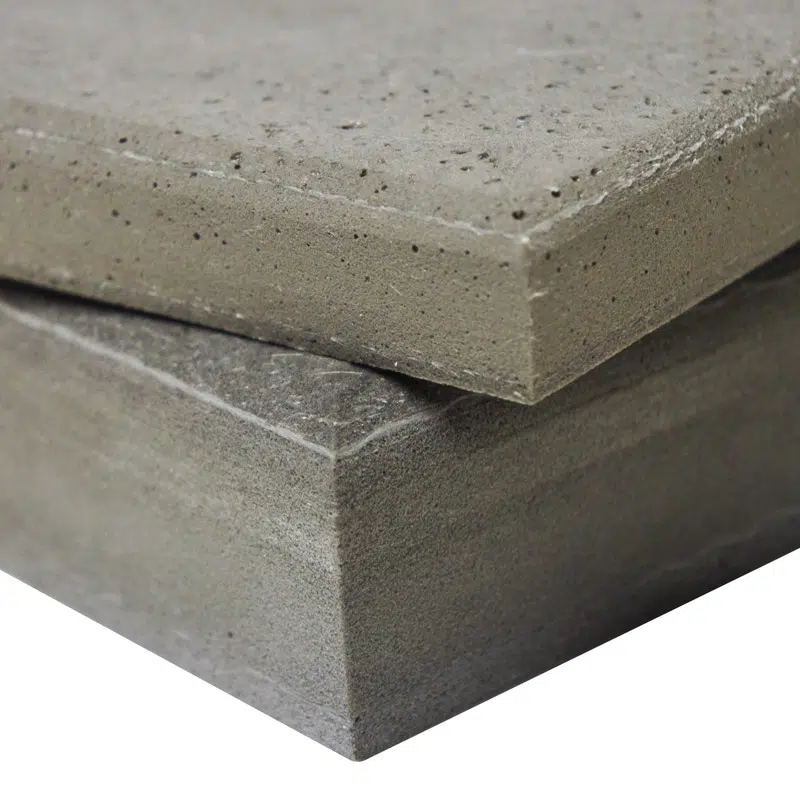
Reinforced Polyurethane
High-density foam composite, lightweight yet strong, ideal for marine and industrial applications.
- Marine decking and flooring
- Boat transoms and bulkheads
- RV and camper construction
- Architectural elements in buildings
- Industrial and transportation components
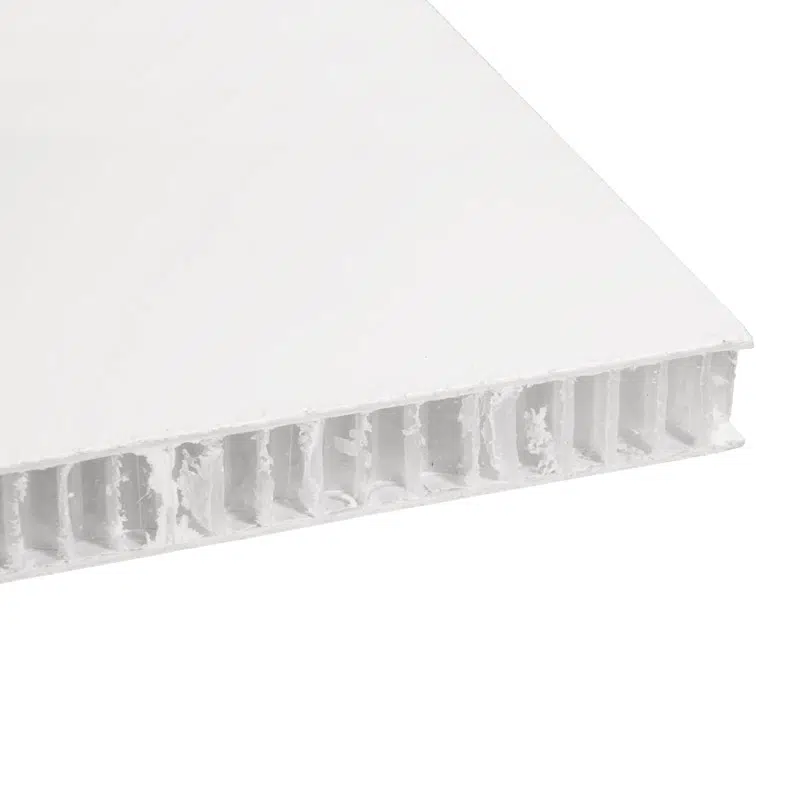
Laminated Honeycomb PP
Lightweight, rigid honeycomb panel, engineered for a range of structural applications.
- Decks and bulkheads in marine manufacturing
- RV floors, walls, and ceilings for weight reduction
- Lightweight structural components in rail and aerospace
- Partitions, walls, roofing, and floors in construction
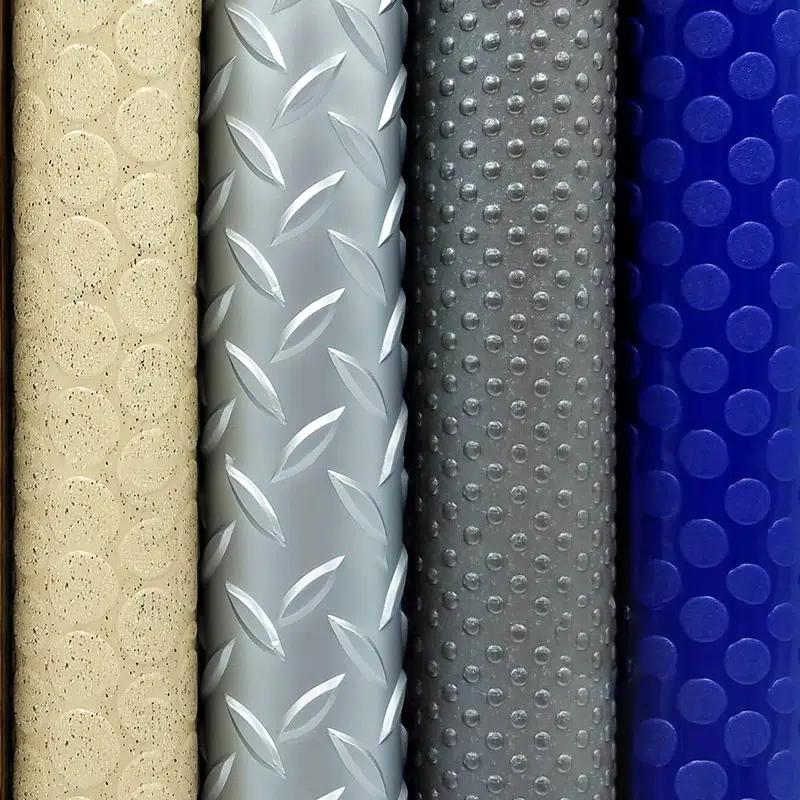
Flexible Vinyl
Durable, waterproof material for flooring, signage, and upholstery, offering easy maintenance.
- Healthcare facilities for hygiene and durability
- Educational institutions for easy maintenance
- Retail spaces for aesthetic versatility
- Marine environments; water-resistant qualities
- Office buildings for cost-effective flooring
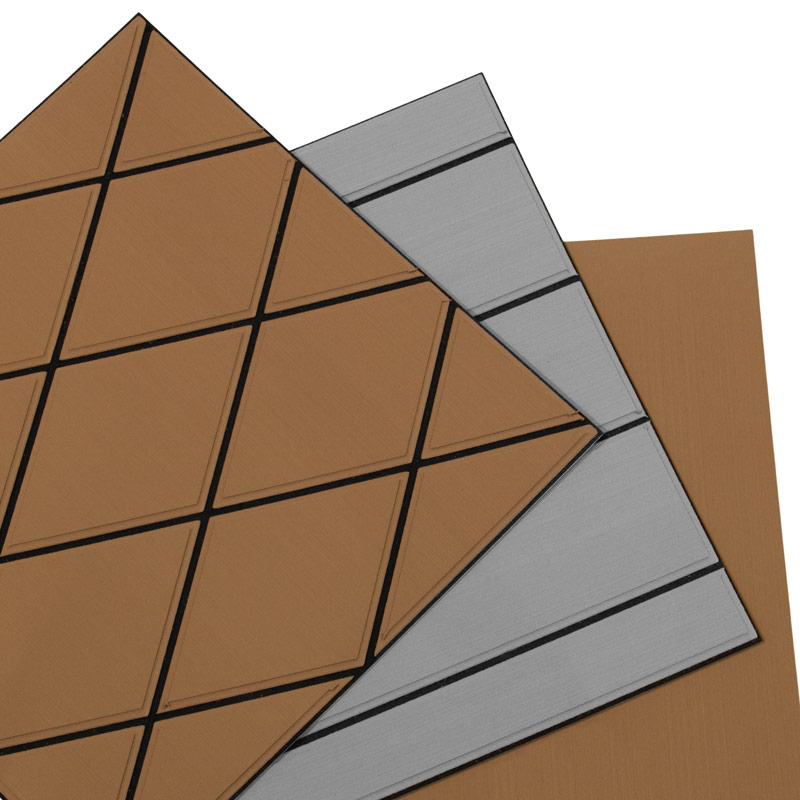
EVA Foam
Attractive, non-slip foam sheets provide comfort, safety, and traction.
- Custom boat decking for comfort and aesthetics
- Shelf liners; provide cushioned surface and keep items from sliding
- Step pads for comfort and traction in high-traffic areas
- Shower seats for a soft non-slip surface
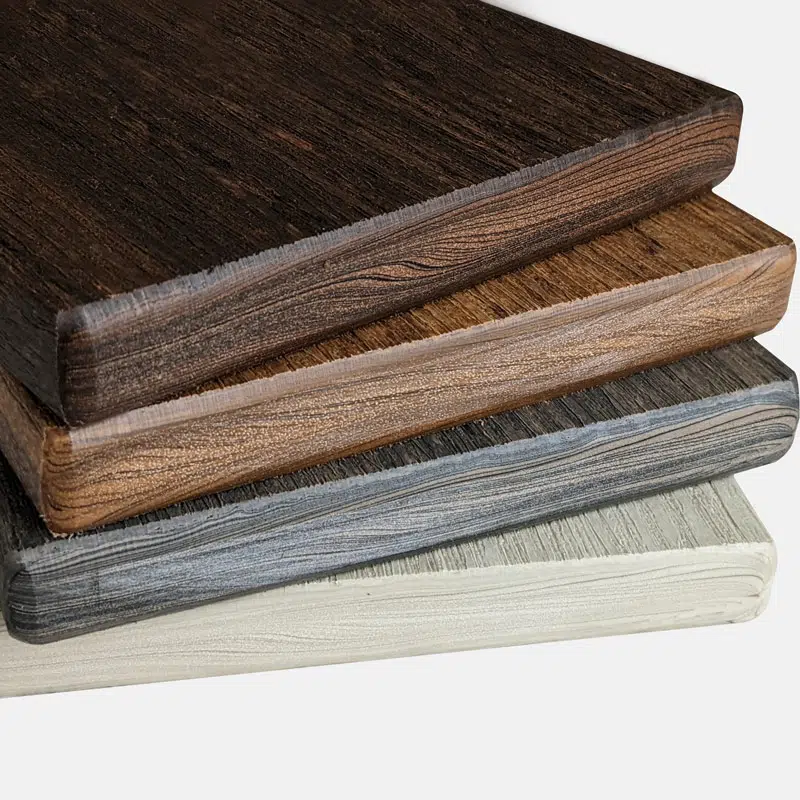
Composite Lumber
Mimics real wood grain, maintenance-free. Perfect for attractive, weather-resistant outdoor furniture.
- Outdoor furniture and playground structures
- Marine docks and boardwalks
- Pergolas and arbors
- Raised garden beds
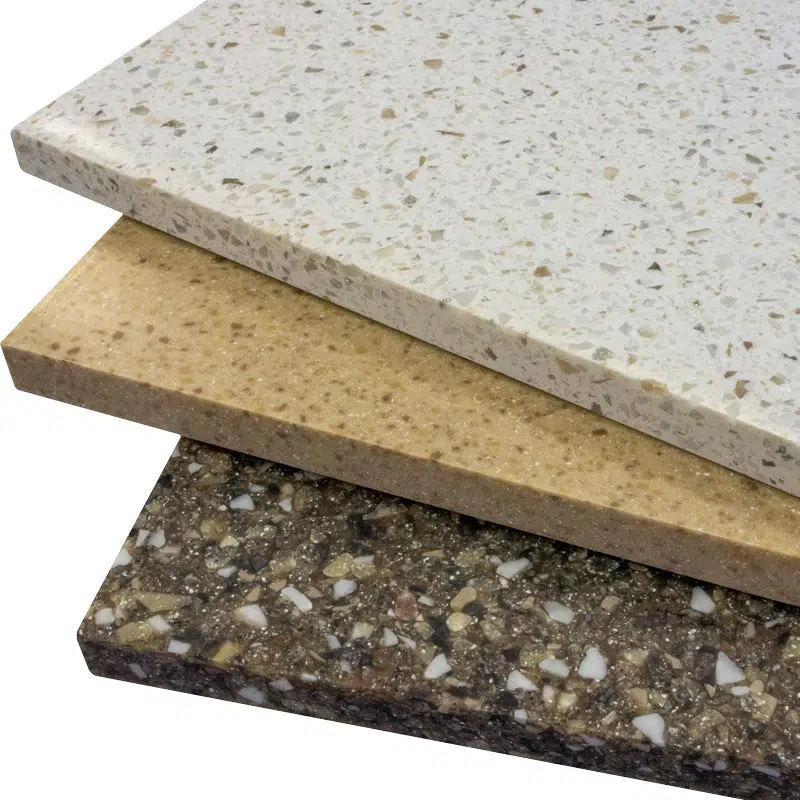
Solid Surface
Seamless and non-porous; ideal for custom countertops, commercial environments and healthcare surfaces.
- Kitchen countertops and backsplashes
- Bathroom vanities and shower surrounds
- Healthcare and dental office surfaces
- Food service counters and tabletops
- Reception desks and office furnishings
- Wall panels and interior cladding
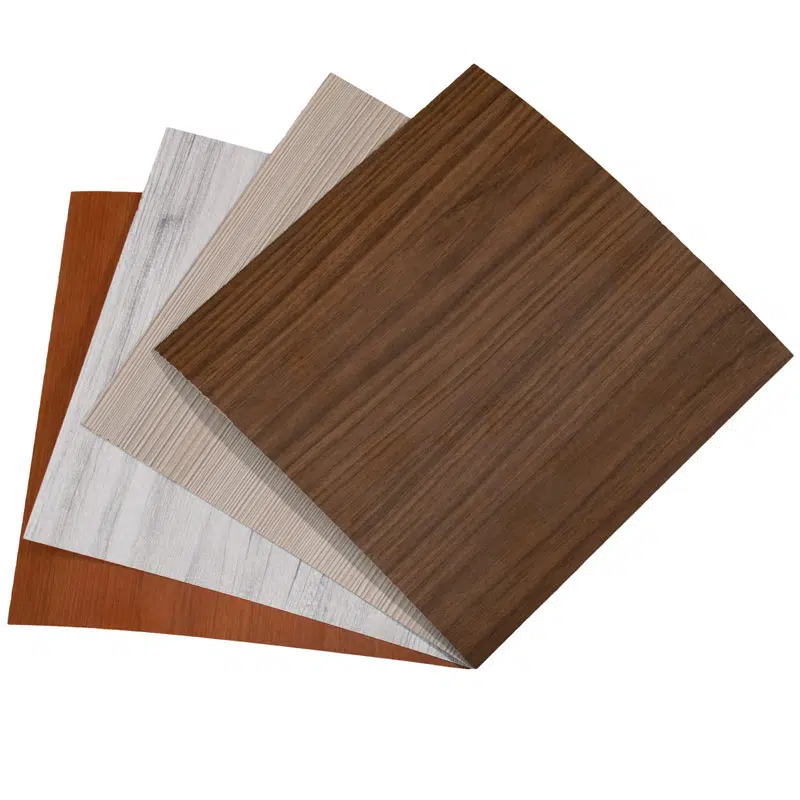
High-Pressure Laminate
Decorative, available in many designs. Easy to clean and maintain; excellent for high-use areas like schools and offices.
- Cabinet surfaces and doors
- Commercial and residential countertops
- Decorative interior surfaces
- Restroom partitions and lockers
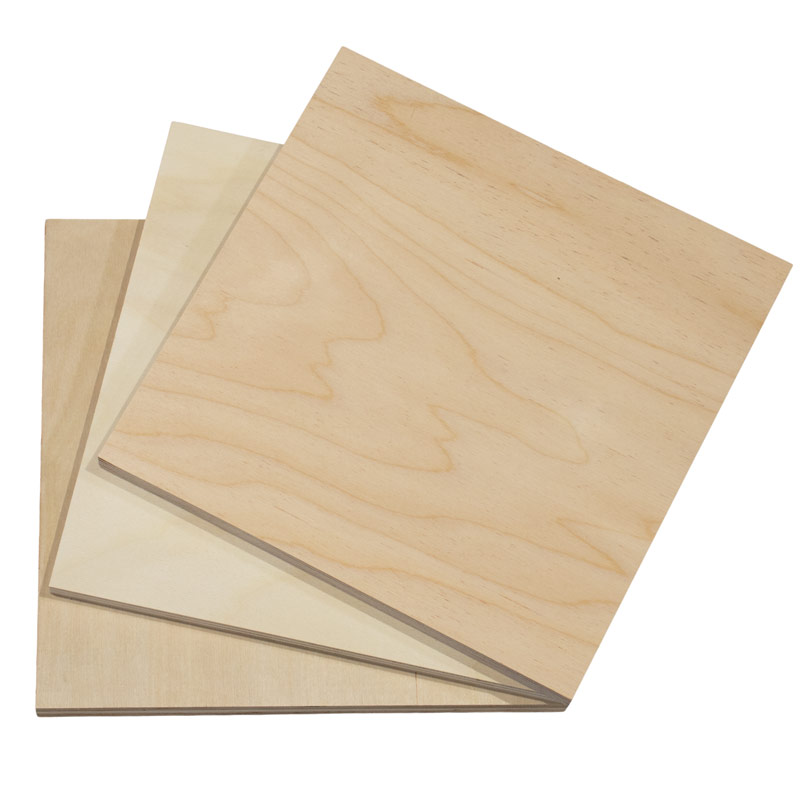
Plywood
Cost-efficient, multi-use material. Great for templates, jigs and budget friendly structural projects.
- Fixtures, jigs, and templates
- Structural underlayment
- Construction framing and sheathing
- Factory work tables and furniture
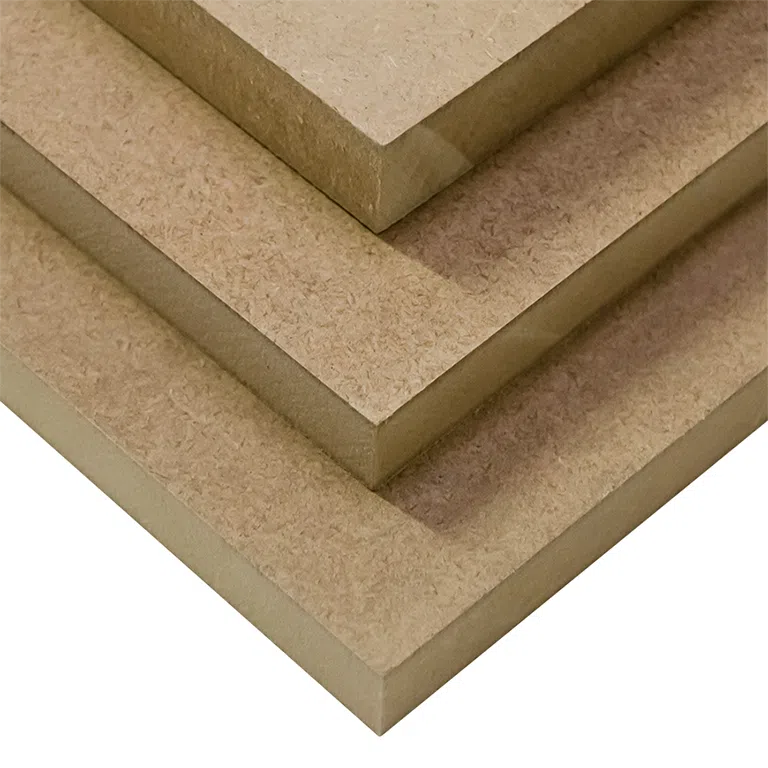
MDF
Consistent density and strength. Smooth surface, easy to paint. Ideal for detailed moldings and millwork.
- Interior carpentry, shelving and furniture building
- Decorative wall panels and wainscoting
- Door and window frames
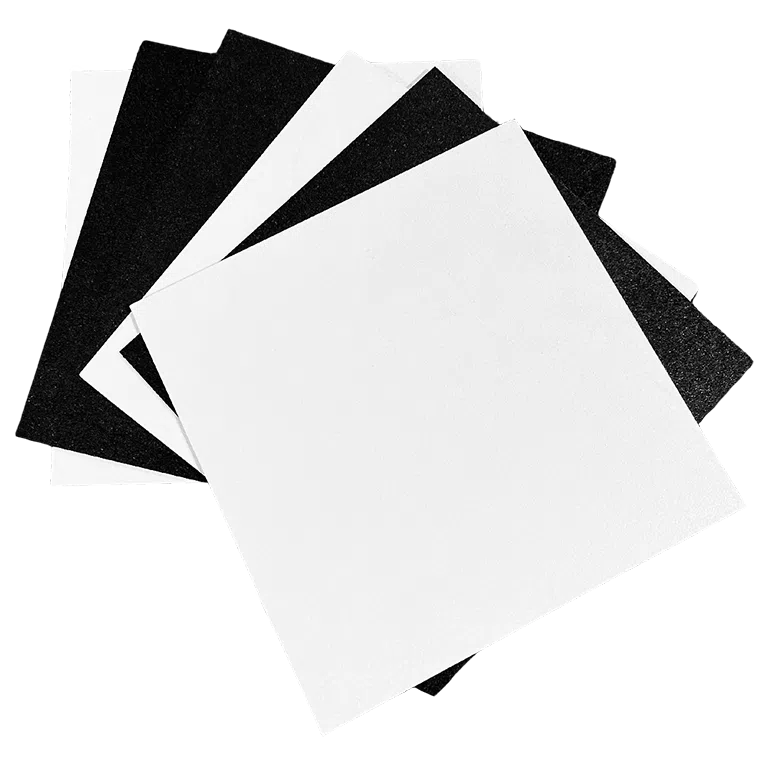
ABS
Cost-effective, thermoformable polymer with a glossy exterior and low moisture absorption.
- Protective casings and electrical enclosures
- Durable signage and point of purchase displays
- Interior automotive panels and trim
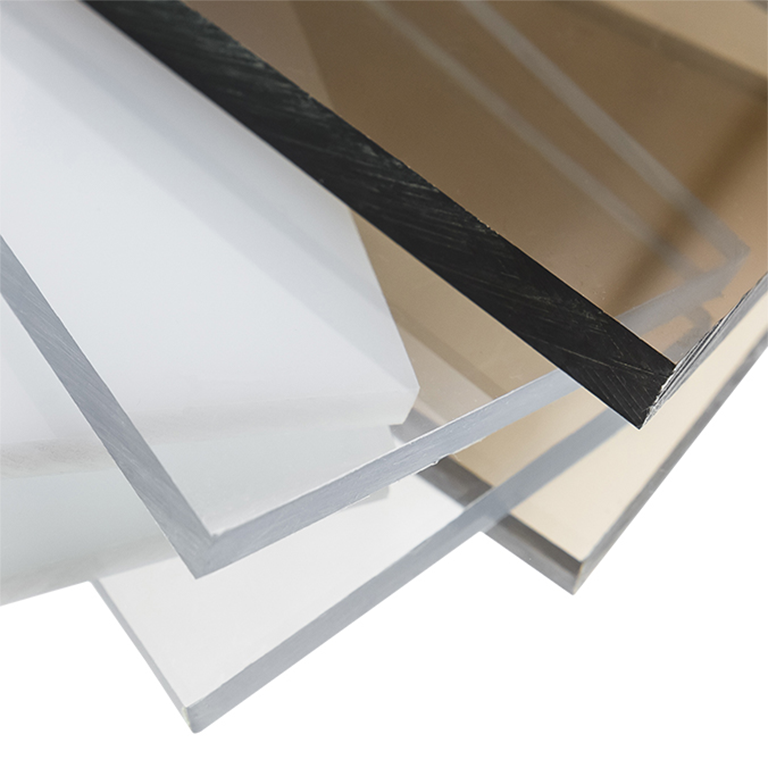
Polycarbonate
A strong, transparent, or opaque plastic, known for its high impact resistance and versatility.
- Machine guards in industrial settings for clear visibility and safety
- Eyewear lenses due to high impact resistance and clarity
- Roofing materials for light transmission and strength
- Bulletproof glass for security in vehicles and buildings
- Automotive components like headlight covers and sunroofs
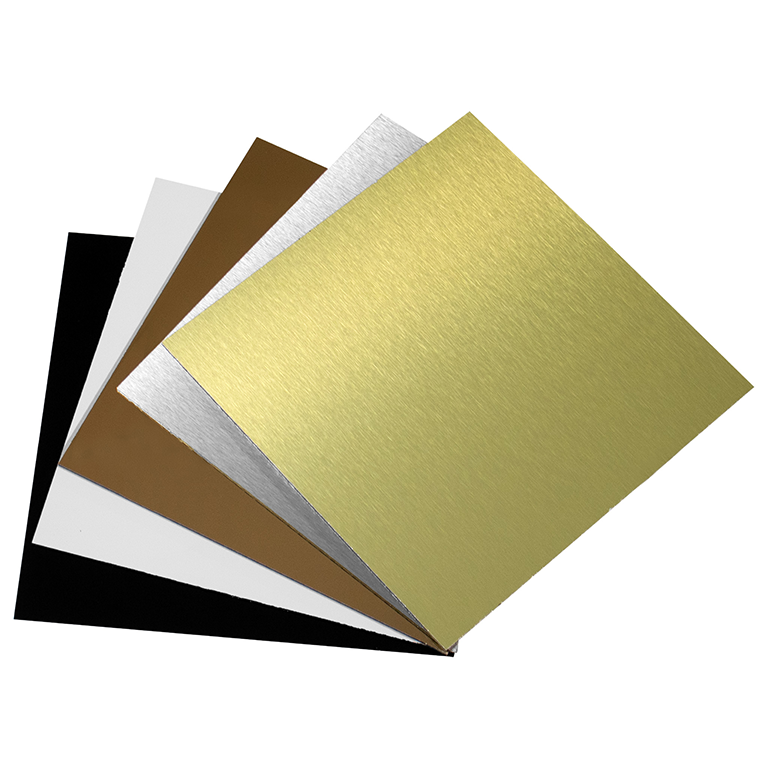
ACM
A durable panel with two metal sheets bonded to a non-metal core, ideal for building cladding and signage.
- Exterior building cladding for commercial and residential structures
- Signage and advertising panels for outdoor and indoor use
- Interior wall panels and partitions in commercial spaces
- Column covers and beam wraps to enhance architectural design
- Vehicle and trailer bodies for lightweight and durable construction
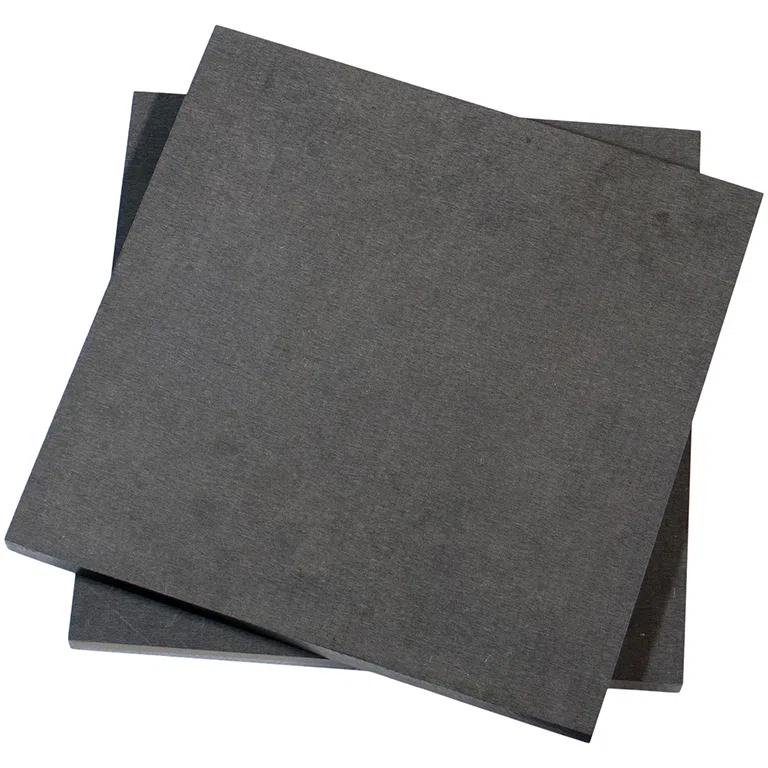
Phenolic
Compact industrial reinforced laminate. Lightweight yet tough — half the weight of aluminum with superior abrasion and impact resistance.
- Backing plate coring material
- Electrical insulators and circuit board substrates
- High-stress mechanical parts such as gears and bearings
- Industrial laminates for harsh environments
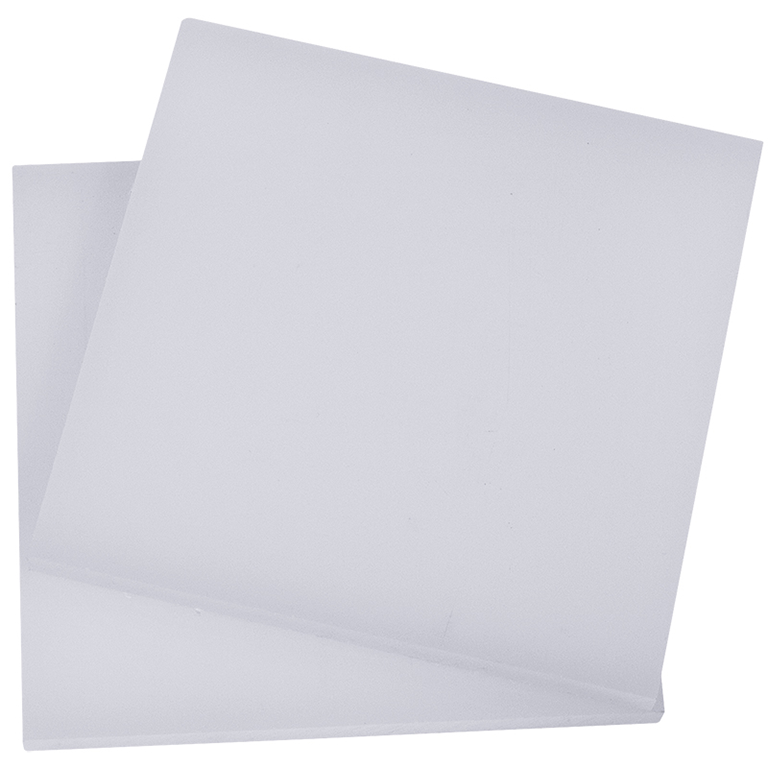
UHMW
Exceptionally durable with high impact strength and low friction; ideal for wear-resistant parts and lining systems.
- Wear strips and slide guides for machinery
- Impact-resistant parts for industrial equipment
- Chute, hopper, and bin liners for material handling
- Bottle and can line machinery components
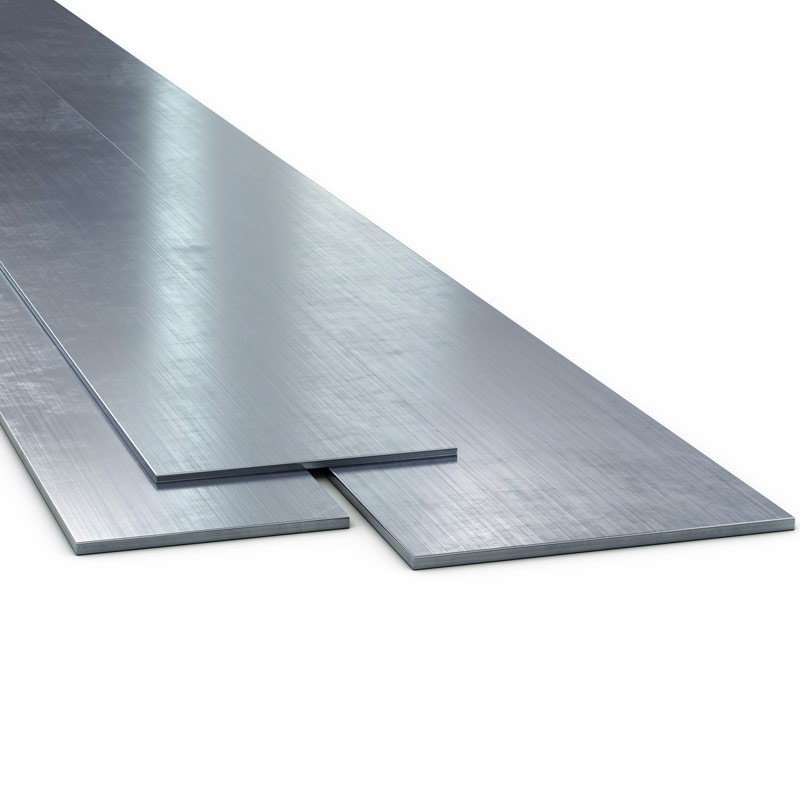
Aluminum
Lightweight and strong; up to 3x lighter than steel. Naturally corrosion-resistant; superior for marine and outdoor applications.
- Door frames for their lightweight and strength
- Marine hardware and fittings resistant to corrosion
- Custom machinery components
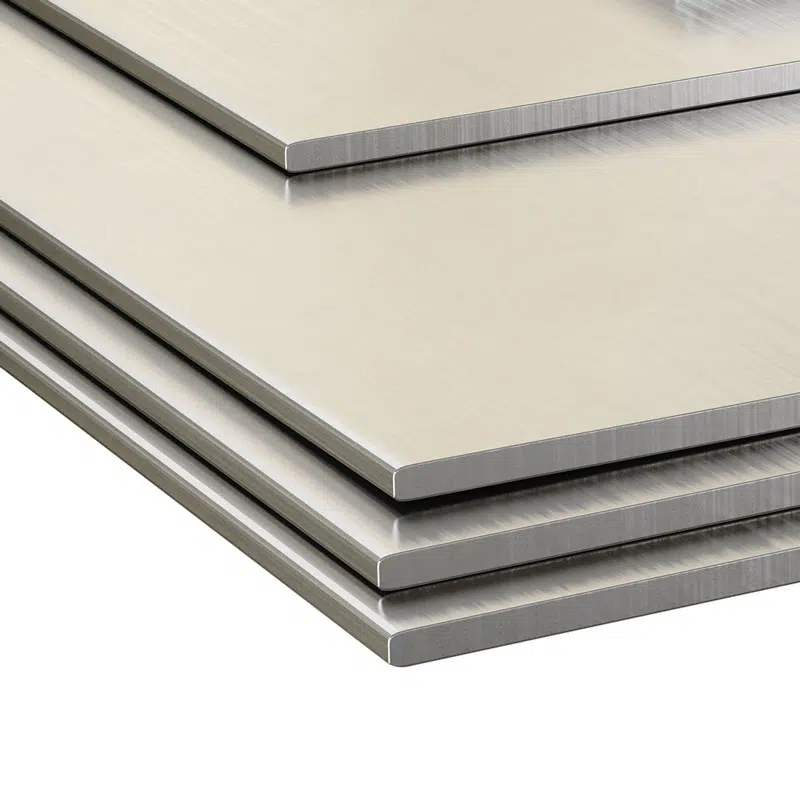
Steel
Cost effective metal (generally less expensive than aluminum) with higher strength and durability.
- Structural components in construction for robust support
- Heavy machinery parts due to high strength and durability
- Automotive frames and chassis components for toughness
- Tools and dies for precision machining and forming
Gallery of CNC Machined Parts
Customer Success Stories
Teak Isle’s Low MOQs Helps HCB Yachts Offer the Customization Options Their Customers Demand
How Teak Isle Helps Godfrey Marine Turn Vision Into Reality and Improve Customers Time on the Water
An Extraordinary Commitment to Customer Service Drives Teak Isle’s Relationship with Everglades Boats
Trusted by Leading Companies
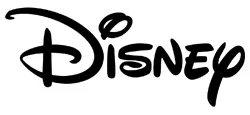
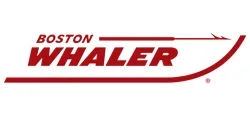
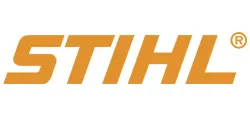
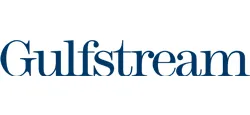
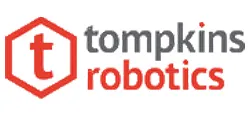
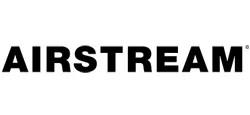
What they're saying...
Hear from our customers, and find out why Teak Isle is the best.
Send us a Message
After hours or prefer to schedule a call? No problem.
Send us a message and we’ll jump right on it.
Call Us Now
Need a partner you can trust to deliver quality on-time parts?
Pick up the phone and chat with a team member now.
(833) 522-5090
Mon-Fri 8am – 4pm (EST)
CNC Machining 101
What is CNC machining?
CNC machining is a manufacturing process in which computers control machines that cut, shape, or drill materials like metal, plastic, and wood. These machines, guided by software, are highly precise and can produce parts consistently – making them ideal for mass production.
By following detailed instructions from a computer program, CNC machines can create complex components used in industries like aerospace, automotive, and electronics. The automation ensures accuracy and efficiency, allowing professional-grade parts to be made quickly without the need for fixtures or manual control.
What materials can be used in CNC machining?
What are the different types of CNC machines?
There are different types of CNC machines, each designed for specific tasks. CNC mills use spinning tools to cut and shape materials. CNC lathes spin the material while a tool shapes it, which is great for making round objects like wheels. CNC routers are similar to mills but are often used for cutting softer materials like wood and plastic. CNC plasma cutters use a hot jet of gas to slice through metal. Each machine is suited to particular jobs, depending on what needs to be made.
What are the advantages of CNC machining over other methods?
CNC machining offers distinct advantages compared to hand machining and injection molding. It’s far more precise and consistent than manual methods, allowing for the repeated production of identical parts without errors. CNC can also handle complex shapes that are difficult to achieve by hand. Unlike injection molding, which requires significant upfront costs for tooling, CNC machining has no expensive mold requirements, making it a better choice for small production runs or prototypes. Overall, CNC machining provides a balance of precision, flexibility, and cost-efficiency across various projects.
How do 3-axis and 5-axis CNC machines differ?
The difference between 3-axis and 5-axis CNC machines is how they move. A 3-axis machine moves in three directions: left to right, front to back, and up and down. This is good for making flat or simple parts. A 5-axis machine can also tilt and rotate, allowing it to reach parts of the material that a 3-axis machine can’t. This makes it possible to create more complex shapes and details in a single step, which is useful for things like airplane parts and sculptures.
What are the typical lead times for CNC machining projects?
Typical lead times for CNC machining projects depend on factors like part complexity, material availability, and production volume. During the prototype process, simple parts may be completed in just a few days, especially if materials are on hand.
More complicated prototypes will take a few weeks – largely dependent on engineering complexity. For ongoing production orders, Teak Isle operates on a standard 3-week lead time. That said, we’ll always go above and beyond where possible to expedite for customers in a unique bind.
How is quality ensured in CNC machining?
At Teak Isle, quality in CNC machining services is ensured through a combination of high-end commercial-grade machines, regular tool maintenance, and strict quality control processes. We frequently change cutting bits to maintain sharpness, ensuring clean and precise cuts.
Additionally, our team follows a rigorous inspection process at various stages of production to verify that parts meet exact specifications. This attention to detail, combined with our advanced machines , allows us to consistently produce high-quality parts with precise tolerances, reducing the likelihood of defects and ensuring customer satisfaction.
What are common applications of CNC machining?
How does CNC machining pricing work?
What software is used in CNC machining?
Why Teak Isle for CNC Machining
Over 40 Years of
Industry Expertise
read more
With over four decades of experience, Teak Isle has built a reputation as a trusted partner in CNC machining. Our extensive knowledge ensures that we deliver high-quality products tailored to the specific needs of a variety of industries, from marine to hospitality.
Cost-Saving Design
and Value Engineering
read more
Our team is committed to helping customers design parts that are not only functional but also cost-effective. Through value engineering, we optimize materials and manufacturing processes to save money without compromising quality or performance.
Direct, Single-Source Manufacturing
from Design to Delivery
read more
At Teak Isle, we manage every stage of your project, from prototyping to production. Unlike companies that outsource to third parties, we handle everything in-house, ensuring a seamless supply chain and consistent quality throughout the entire process.
U.S.-Based Production
and Sales
read more
All our production and sales operations are located in the United States. This allows us to provide faster lead times, reliable communication, and the ability to meet tight deadlines without relying on overseas suppliers.
Extensive In-House
Material Inventory
read more
Teak Isle offers a vast in-house stock CNC material selection, allowing us to quickly source and manufacture your parts. By utilizing our robust inventory, we help customers avoid the added costs and delays associated with special material orders.
Comprehensive In-House
Finishing and Assembly
read more
We go beyond CNC machining by offering full finishing and assembly services. From polishing and painting to complete assembly, Teak Isle ensures that your products arrive ready for use, simplifying your supply chain and reducing overall project costs.
CNC Machining Pros & Cons
Pros
High Precision and Consistency in Production
CNC machining ensures precise and consistent results, maintaining tight tolerances across production runs. This high level of accuracy is crucial for parts that need to fit perfectly together or meet exact specifications, ensuring consistent quality in every piece produced.
Versatility in Material and Design
CNC machines can work with a wide variety of materials, including metals, plastics, wood, and composites. This flexibility, combined with the ability to produce complex geometries, makes CNC machining suitable for diverse industries and applications.
Scalability for Production
CNC machining easily adapts from single prototype runs to large-scale production, allowing manufacturers to scale production based on demand. The same machine can be reprogrammed to produce varying quantities, making it highly flexible for different project sizes.
Cost-Effective for Small-Mid Size Batches
CNC machining is ideal for small to mid-sized production runs because it doesn’t require expensive molds or extensive setup. This makes it an affordable option for producing high-quality parts without the large upfront costs typically associated with other manufacturing methods.
Quick Turnaround for Design Changes
CNC machines can be quickly reprogrammed to accommodate design modifications, allowing for fast adjustments with minimal downtime. This capability is particularly valuable during prototyping or when iterative design improvements are needed.
Cons
Material Waste/Scrap
CNC machining is a subtractive process, which means excess material is cut away during production. This can result in material waste, particularly with expensive materials, impacting overall cost efficiency.
Higher Costs for Large Production Runs
For very large volume manufacturing, CNC machining may not be cost-effective compared to methods like injection molding, where the per-part cost decreases significantly after the initial setup.
Size Constraints & Sheet Size Considerations
Fitting parts within standard sheet sizes improves material yield and lowers costs. Larger components may face machine size limits, needing additional setups that add time and expense.